NatQuest SCM Genius Team, 7th April 2025
In the world of business today, procurement has evolved far beyond a transactional function. It is now a strategic enabler of resilience, value creation, and operational continuity. As global supply chains become more fragmented, outsourced, and exposed to disruption, the role of Business Continuity Planning (BCP) and Disaster Control Planning (DCP) within procurement is gaining critical importance. From pandemic-induced shortages to geopolitical shocks and cyber threats, organisations must now design their procurement strategies not just for efficiency, but for continuity.
Economic and political instabilities exacerbate these challenges. Trade wars, fluctuating currency rates, and shifting regulatory environments can wreak havoc on supply chains, leading to increased costs, delays, and reputational risks. Political unrest or sanctions can disrupt critical supply routes, while economic downturns can impact supplier solvency and lead to unexpected shortages. Amid such uncertainties, a robust BCP and DCP framework within procurement ensures that companies remain agile and responsive. This enables them to sustain operations and maintain service levels, even in the face of severe disruptions.
Furthermore, incorporating continuity planning into procurement helps businesses leverage opportunities arising from market shifts. By proactively managing risks, organisations can secure alternative suppliers, diversify their sourcing strategies, and negotiate better terms. This not only mitigates the impact of disruptions but also drives competitive advantage and long-term sustainability.
Ultimately, the integration of BCP and DCP into procurement transforms the function into a cornerstone of organisational resilience. It ensures that the company can navigate both anticipated and unforeseen challenges with confidence, safeguarding its ability to deliver value to customers and stakeholders continuously.
BCP and DCP Procurement
Business Continuity Planning (BCP)
BCP refers to the systematic process of identifying risks to supply operations and establishing policies and structures to ensure that essential procurement activities can continue during and after a disruptive event. BCP in procurement focuses on:
- Sustaining critical sourcing operations
- Ensuring supplier performance under adverse conditions
- Maintaining supply chain visibility and governance
- Preserving customer service levels
Disaster Control Planning (DCP)
DCP, often considered a subset of BCP, is a tactical response framework designed to contain and recover from sudden, high-impact disruptions. In procurement, this might involve supplier insolvency, warehouse fires, transport strikes, or regulatory embargoes. DCP addresses:
- Incident response protocols
- Communication workflows
- Rapid sourcing and rerouting procedures
- Stakeholder coordination
Together, BCP and DCP help procurement leaders move from reactive firefighting to proactive resilience-building.
Procurement Must Lead on Continuity Planning
Procurement is uniquely positioned to shape the organisation’s exposure to external risk. Unlike internal departments, it operates at the interface of the company and its extended supplier ecosystem. It has visibility over:
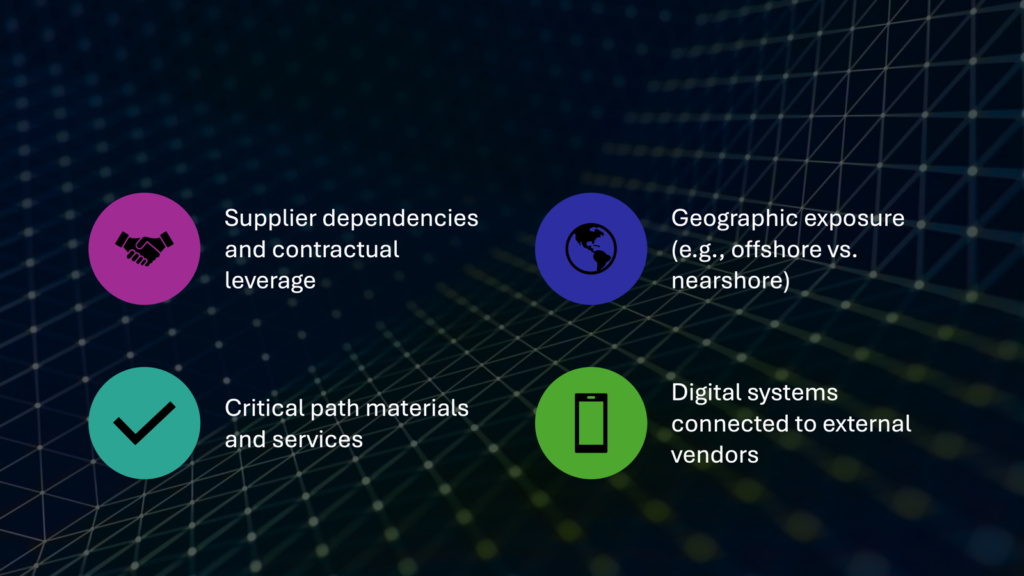
This external lens means procurement should not be an afterthought in continuity planning—it should be the core architect of supply-side resilience.
Strategic Objectives of BCP and DCP in Procurement
- Ensure Operational Uptime: Avoid disruptions to production or service delivery caused by material shortages or supplier failure.
- Preserve Customer Trust: Protect the customer experience by ensuring consistency in product availability, delivery timelines, and service standards—even during disruptions.
- Maintain Regulatory Compliance: Avoid penalties and breaches related to late deliveries, contract non-performance, or unethical sourcing during emergencies.
- Safeguard Financial Stability: Minimise revenue loss, working capital stress, and unplanned cost escalations arising from crisis conditions.
- Protect Brand Reputation: Manage supplier risks (e.g., forced labour, environmental violations) that may surface under scrutiny during a crisis.
Core Components of a Procurement-Focused BCP/DCP
Component | Description |
Risk Segmentation | Categorise suppliers by criticality, spend, and risk exposure (e.g., sole source, overseas, political hotspots). |
Alternate Sourcing | Prequalify and contract secondary suppliers or marketplaces for contingency fulfilment. |
Contractual Safeguards | Embed BCP clauses, SLAs, force majeure definitions, and early termination rights. |
Continuity Audits | Assess vendors on their BCP maturity and incident response readiness. |
Digital Scenario Modelling | Use supply chain platforms to simulate disruptions and assess mitigation paths. |
Communication Protocols | Define who communicates what, when, and how during a disruption. |
Recovery Plans | Detail the timeline, resource allocation, and workflows for supplier switching, rerouting, and restocking. |
Digital Enablers of Continuity
In the composable, API-driven digital era, BCP and DCP are no longer spreadsheet exercises. Organisations are increasingly using platforms like NatQuest SCM Genius to manage continuity across procurement and supply operations.
How NatQuest SCM Genius Supports Continuity Planning:
- Real-time risk visibility on suppliers, categories, and geographies
- Expert-led continuity planning tailored to S&OP and sourcing strategies
- Playbooks and workflows for rapid execution of continuity actions
- Scenario modelling tools to test supplier failure or port closures
- Integration with ERP/TMS platforms to enable live data access during disruptions
This aligns with a broader industry shift away from static consulting reports and towards outcome-driven, platform-enabled continuity services.
Procurement Use Cases for BCP and DCP
Single-Source Risk Mitigation
For critical components sourced from a single supplier, BCP requires identifying potential alternative manufacturers, testing their capabilities, and negotiating contingency terms in advance.
Geopolitical Risk Planning
Procurement leaders must anticipate trade disruptions, such as sanctions or border delays. BCP enables rapid pivoting to nearshore vendors or restructured routing.
Cybersecurity and IT Integration Risks
As suppliers increasingly access internal systems, DCP involves defining emergency access cut-off protocols, forensic supplier audits, and disaster recovery for digital supply networks.
Natural Disaster Preparedness
From floods to earthquakes, procurement must plan for physical disruptions in source countries by securing buffer stock, diverse suppliers, and regionalised fulfilment centres.
From Policy to Practice: Making BCP a Procurement Standard
Integrating BCP and DCP into procurement means shifting culture, systems, and processes. Key actions include:
- Making continuity planning part of supplier onboarding
- Aligning procurement scorecards with continuity readiness
- Training sourcing managers in incident response protocols
- Embedding continuity assessments into category strategies
- Reporting BCP risk levels at board or ESG committee level
Conclusion
In the post-pandemic, pre-AI supply chain era, the companies that thrive are those that plan for the unplanned. Procurement plays a critical role in ensuring that the organisation can source, produce, and deliver—regardless of disruption. By embedding business continuity and disaster control planning into procurement strategy—supported by platforms like NatQuest SCM Genius—enterprises can move beyond cost optimisation and become truly resilient, responsive, and future-ready.